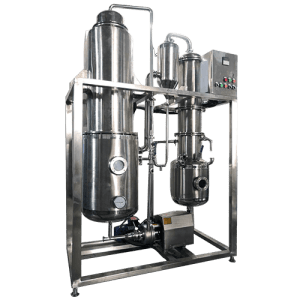
Though suitable for materials with higher concentration and higher viscosity, a falling film evaporator still needs to be cleaned after using for a long time. As the production time prolongs, a falling film evaporator may produce scaling or coking. The degree of scaling and coking varies with different material properties and different evaporation concentrations. Therefore, a falling film evaporator is required to shut down for cleaning after a certain period of time. Otherwise, it will become time-consuming and even difficult to clean thoroughly, which will influence product quality ultimately. So how to clean a falling film evaporator?
Chemical Cleaning of Evaporators
Cleaning is one of the most essential parts in evaporators’ using. Because a high-quality cleaning can guarantee the quality of evaporators’ working, which is related to the extraction and concentration of sample substances. The evaporator circulating cooling water contains a large amount of salt substances, corrosion products and various microorganisms. Since it is not treated with water, the evaporator will run for a period of time and there will be a large amount of calcium, magnesium carbonate scales,algae ,sludge, slime,and microorganisms on the water side, which adhere firmly to the inner surface of the copper tube, resulting in deterioration of heat transfer. It will increase in circulating pressure, lower the vacuum of the unit, affect the operating efficiency of the unit, and result in economic loss of production. Therefore, a good cleaning of evaporators is necessary. Among the cleaning ways of evaporators, chemical cleaning is one of the most efficient cleaning way, which includes the selection of cleaning agent, the establishment of cleaning system and cleaning process.
Vertical Falling Film Evaporators’ Cleaning System
Even though the cleaning system of the falling film evaporator is very efficient, there still are some parts could get better, as follows:
1. Improve the equipment structure. According to the data analysis, it will be more efficient for the cleaning system to add a steam mixer, which can mix different kinds of steams before they come into evaporators.
2. Make sure the equipment run at minimum load. Clean the device membrane maker regularly, so that the inner tube wall of falling film evaporators runs under the over of liquid film.
3. Add a rainer on the high-temperature steam inlet nozzle.
4. Decrease the cleaning system’s stress level. Because stress corrosion happens at a certain stress level, we could increase the thickness of the connection tube wall in order to decrease peak stress index and stress level, so that the stress level is not enough for having a stress corrosion.
5. Enhance the management of operating to prevent lye or abnormal steam with lye going through, which could ruin the special environment for stress corrosion.
[title text=”Related Products” tag_name=”h2″ color=”rgba(32, 163, 219, 0.81)”]
-
FFE 200L Single-Effect Falling Film Evaporator
Read more -
20L Falling Film Evaporator
Read more -
50L Single-Effect Falling Film Evaporator
Read more -
S212-200L Double-Layer Glass Reactor
Read more -
DLSB-200/40 Low Temperature Coolant Circulation Pump(Chiller)
Read more -
R-1020 Double Cold Trap Rotary Evaporator
Read more
[title text=”Related Posts” tag_name=”h2″ color=”rgba(32, 163, 219, 0.81)”]
https://www.rotovap.cn/falling-film-evaporator-problems/3661.html
https://www.rotovap.cn/falling-film-evaporator-problems/3543.html
https://www.rotovap.cn/falling-film-evaporator-problems/3579.html
https://www.rotovap.cn/falling-film-evaporator-problems/3160.html
https://www.rotovap.cn/falling-film-evaporator-problems/3693.html