In the industrial field, there are always some substances which need to be extracted or concentrated. Therefore, there are also so many devices or techniques for achieving the extraction or concentration of substances, such as falling film evaporators. A falling film evaporator refers to a concentration and evaporation device used in industries, which has high heat transfer efficiency, small temperature difference, short residence time of material, no deterioration, low pressure drop, easy operation, low energy consumption, small equipment size, etc.
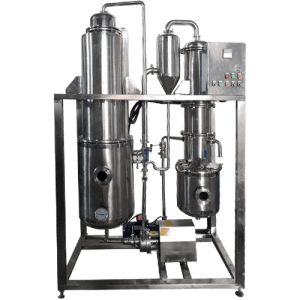
Working Principle of a Falling Film Evaporator
A Falling film evaporator is an efficient one-way non-circulating membrane evaporator. Its working principle makes it has the characteristics of high heat transfer efficiency, low temperature difference loss, short heating time, non-deterioration, easy multi-effect operation, low energy consumption and small equipment volume. It is widely used in chemical industry, medicine, light industry and food industry.
The working principle of falling film evaporators can be described as follows. The liquid is added to the upper tube of the heating chamber of the falling film evaporator. Through the liquid distribution and film forming device, it is evenly distributed into the heat exchange tubes. Under the action of gravity and vacuum induction and air flow, it forms a uniform film from the top to the bottom. During the flow, it is heated and vaporized by the shell-side heating medium. The generated steam and the liquid phase enter the separation chamber of the evaporator. The vapor-liquid is sufficiently separated, and the steam enters the condenser for condensation (single-effect operation) or enters the next-effect evaporator. The medium is heated to achieve multi-effect operation, and the liquid phase is discharged from the separation chamber.
Operation Procedures of a Falling Film Evaporator
- The first step is to remove the gas in the equipment to create a vacuum environment and after the vacuum degree is enough, feed water in replacing materials. When water is running smoothly (the water in the evaporator increases with the increasing in walk, surface evaporation indoor materials are not higher than sight glasses), open circulating pump, cooling water is piped in, start the heating tube and start the discharge pump. After the equipment runs well, adjust throttling components in each position according to the the random process flow chart of the equipment. Then replace the material with water for running. When the vacuum degree and temperature difference meet the requirements, replace the material with water for running for more than 4 hours. It is qualified if the evaporation capacity meets the requirements; otherwise, adjust the throttle element again.
- Firstly start the vacuum pump. If it is a water ring vacuum pump, the water ring vacuum pump should be started at no load. After the water ring vacuum pump is running normally, the working water valve of the water ring pump is opened. When the vacuum and temperature difference of each effect reach the required level, water should be used instead of the material to start the operation and start the condensate. After the water is cut off, the material is put into the material tank. The sampling valve is initially opened, the water is discharged, and the material that does not meet the concentration requirement is placed in the tank. When the discharge concentration requirement is reached, the discharge valve is opened, and the sampling valve on the material tank is closed, and the equipment is put into normal operation.
- During the operation of the pump and before starting, it should be observed that the cooling water of the mechanical seal of the pump must not be interrupted, so as not to damage the mechanical seal of the pump.
- When the work is to be stopped, water is used instead of the material to replace the materials in the equipment and its piping to prevent the material from crystallizing or solidifying in the equipment and its piping. When the ambient temperature of the equipment is below 0 °C, the water in the equipment and its pipeline should be drained to avoid freezing or blocking the pipeline.
- When parking due to accidents such as sudden power failure, immediately close the valve, release the materials stored in the equipment and its pipeline as soon as possible, or dilute the heated water until it does not crystallize or solidify. When there is material in the equipment and its pipeline, the material pump should be started first to make the material run smoothly when starting the vehicle, and then the vacuum pump is started.
- During the operation, if the degree of vacuum is low, especially after restarting after accidental parking caused by power failure and so on, immediately find out if there is leakage at the flange and the joint, and block the leak in time.
- The cleaning of equipment: After the equipment is finished, the equipment and its pipelines are washed and cleaned with water, 1-2% NaoH aqueous solution, clean water, 1-2% HNO3 aqueous solution and clean water. The pump is pumped with the above washing liquid, and each washing liquid should not be less than 10 minutes.
The equipment should not be washed by using hydrochloric acid or hydrochloric acid chloride-containing aqueous solution during scouring or cleaning to avoid intergranular corrosion of stainless steel equipment and affect the service life of the equipment.
Constructions of a Falling Film Evaporator
The falling film evaporator system mainly consists of several parts.
The first part is the evaporator (the heat exchanger), which is used to heat and evaporate liquid materials.
The second part is the separator, mainly used to separate the concentrated liquid and the secondary steam generated after heating.
The third part is the preheater, which is used to preheat liquid materials entering the steam and cool the secondary steam in order to recycle and utilize it.
The fourth part is the condenser, whose function is to condense the secondary steam so that it can be recycled and utilized.
The fifth part is the condensate tank, which is connected to the pump at the outlet and capable of discharging condensate liquid automatically.
Applications of a Falling Film Evaporator
As the highly efficient evaporation equipment, falling film evaporators are more and more well-received. It’s widely used in a great number of fields, such as the pharmaceutical, food, chemical, light fields and other fields for the evaporation and concentration of water and organic solvents. And falling film evaporators are especially suitable for the evaporation and concentration of thermal sensitive materials. It can operate continuously under the conditions of vacuum and low temperature, featuring the high evaporation efficiency, energy conservation and low operating cost. As well, materials can be ensured not to change easily during the evaporation. In the following parts, the main applicable fields of falling film evaporators will be introduced in detail.
[title text=”Related Products” tag_name=”h2″ color=”rgba(32, 163, 219, 0.81)”]
-
FFE 200L Single-Effect Falling Film Evaporator
Read more -
20L Falling Film Evaporator
Read more -
50L Single-Effect Falling Film Evaporator
Read more -
S212-200L Double-Layer Glass Reactor
Read more -
DLSB-200/40 Low Temperature Coolant Circulation Pump(Chiller)
Read more -
R-1020 Double Cold Trap Rotary Evaporator
Read more
[title text=”Related Posts” tag_name=”h2″ color=”rgba(32, 163, 219, 0.81)”]
https://www.rotovap.cn/falling-film-evaporator-problems/3661.html
https://www.rotovap.cn/falling-film-evaporator-problems/3579.html
https://www.rotovap.cn/falling-film-evaporator-problems/3160.html
https://www.rotovap.cn/falling-film-evaporator-problems/3693.html