A spray dryer is a commonly used drying device to transform liquid materials into powder or granular form. Its working principle can be broken down into the following key steps:
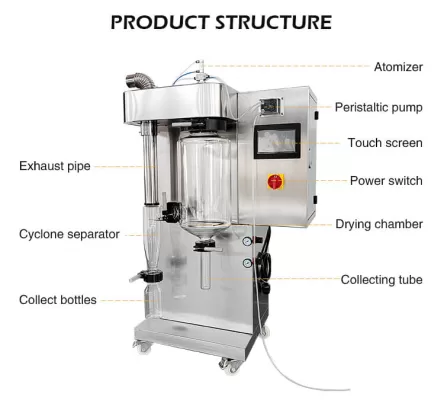
1. Atomization: Initially, the liquid material is introduced into the spray chamber of the spray dryer. This liquid material can be a solution, suspension, or emulsion, typically containing solid particles or dissolved substances. The liquid material is atomized by the spray system, converting it into tiny liquid droplets sprayed into the chamber.
2. Hot Air Supply: Inside the spray chamber, hot air or nitrogen is supplied at high temperatures. This hot airflow aids in the rapid evaporation of the solvent in the spray, leaving behind the solid portion. The temperature of the hot air is typically adjusted according to the nature of the material and process requirements to ensure controlled evaporation.
3. Drying of Wet Liquid Droplets: Within the hot airflow, the tiny liquid droplets start to evaporate, transforming into solid particles. At this stage, the surface area of the droplets is relatively large, resulting in a fast evaporation rate. In the drying chamber, particles become smaller and smaller until they ultimately take the form of powder or granules.
4. Separation of Solid Particles: Once the liquid has completely evaporated, the obtained solid particles are conveyed to a separation device, often a cyclone separator. Here, solid particles are separated based on their size and density, with larger particles collected by gravity or the airflow of the cyclone separator, while smaller particles are carried into the exhaust gas treatment system.
In summary, the working principle of a spray dryer can be summarized as the atomization of liquid material into tiny liquid droplets, rapid evaporation within a hot airflow, and the eventual production of the desired powder or granular product. This process is commonly used in the production of food, pharmaceuticals, chemicals, and other granular products to enhance their storage stability, solubility, and usability. Careful control of process parameters is crucial to achieving the desired product characteristics, necessitating the monitoring of temperature, humidity, airflow velocity, and other process parameters.