Description
PP series industreal centrifuge can be used to extract and filter centrifuges for cannabis and other plants. The series of centrifuges extract the active ingredients in plants through a built-in program, which is single-handed, easy to use and large in capacity.
The industrial centrifuge adopts a closed structure, and the seal is made of PTFE; The explosion-proof motor, frequency changer, PLC, touch screen and other devices can be used to achieve the sealed explosion-proof requirements.
Industrial centrifuge can be used to extract and filter centrifuges for cannabis and other plants. The series of centrifuges extract the active ingredients in plants through a built-in program, which is single-handed, easy to use and large in capacity.
Working Principle
The operator fills the filter bag with ground plant material and places it in the machine. Then, ethanol is added until the plant material is submerged, and the program is set to bidirectional (positive and reverse alternating) rotation to fully extract the active ingredients in the plant. The bottom valve is opened to release the extract, and then the plant material is subjected to high-speed rotary exhaustion of fluid to completely recover the extract.
Product Parameters
Model | Drum diameter (mm) | Drum height (mm) |
Volume (L) | Revolving speed (r/min) |
Motor Power (KW) |
Size (mm) | Weight (KG) |
PP-15 | 300 | 250 | 15 | 2000 | 1.1 | 950*500*480 | 210 |
PP-25 | 300 | 350 | 25 | 2000 | 1.5 | 950*500*580 | 220 |
PP-45 | 450 | 300 | 45 | 1500 | 2.2 | 1250*700*760 | 450 |
PP-60 | 450 | 400 | 60 | 1500 | 3 | 1250*700*860 | 470 |
PP-85 | 600 | 300 | 85 | 1250 | 3 | 1500*900*950 | 970 |
PP-110 | 600 | 400 | 110 | 1250 | 4 | 1500*900*1050 | 1000 |
PP-140 | 600 | 500 | 140 | 1250 | 5.5 | 1500*900*1150 | 1030 |
Installation & Adjustment
1.The machine must be kept in storage before and after installation. Pay attention to the moisture protection of the motor and pay attention to the protection of the electronic control system.
2.Safety must be taken during lifting to prevent the machine from being damaged by collision.
3.The centrifuge installation must be horizontal and the reference surface is the upper plane of the machine base (level ≤ 3mm).
4.There should be sufficient space between the equipment and other equipment installed adjacent to the centrifuge and the centrifuge to prevent the machine from colliding with it and causing damage or noise, and to facilitate inspection and maintenance of the machine.The space required for the use and maintenance of the centrifuge should be considered during the installation position of the centrifuge.There should be a pedestrian passage of not less than 1 meter around the centrifuge main unit. There must be more than 2 meters of assembly and disassembly maintenance space above the centrifuge main unit.
5.Because the centrifuge has slight vibration during high-speed operation, the pipe (feeding pipe, outlet pipe, washing pipe, exhaust pipe, cable pipe, etc.) connected to the centrifuge must be flexibly connected, and the connection must be reliable. Sealed or insulated to ensure no leakage and safe use of electricity. The diameter of the external outlet pipe shall not be less than the diameter of the machine outlet pipe, and shall not have dead bends or blockages. The pipe arrangement shall be lower than the height of the outlet pipe outlet and have a certain height difference so that the liquid discharge is unblocked.
The Size of Pipe Interface
Model Program | Model | ||
PP-15/PP-25 | PP-45/PP-60 | PP-85/PP-110/PP-140 | |
Feed nozzle diameter (mm) | 19 | 32 | 51 |
Washing nozzle diameter (mm) | 19 | 19 | 19 |
Outlet nozzle diameter (mm) | 51 | 51 | 76 |
Cooling tube diameter (mm) | 19 50 50 |
Precautions for Use
1.Select the appropriate filter cloth type to make the filter bag according to the characteristics of the separated materials. And ensure the filter bag and the drum body have a good fit according to the filter bag provided by the manufacturer.
2.The electrical wiring is connected by an electrician according to the electrical control schematic diagram of the PP series centrifuge to wait for the operation and adjustment of the centrifuge.
3.After the centrifuge is installed, turn on the motor power, adjust the tension of the motor’s V-belt, and prepare for the test run.
Warnings
7.1 The cover must be covered and locked before the machine is running!
7.2 Do not open the cover when the machine is running!
7.3 It is strictly forbidden to use rigid connection among the feeding tube, the washing tube and the liquid discharging tube on the main machine of the centrifuge, so as not to affect the vibration damping system of the main machine itself and damage the machine.
Industrial Centrifuge Used
1 Power supply and motor
a. Power supply: three-phase or single-phase 220V/60Hz; see the technical parameters for motor power.
b. The motor must be grounded reliably to ensure safe use of electricity.
c. The connection between the centrifuge and the power source is wired according to the electrical control schematic diagram (Fig. 3). The electrical model and specifications are configured according to the motor power and rated current, and are configured according to the relevant electrical control standards to prevent electrical overload and effective. Implement overload protection.
2 Drag and control
a. The drum of the centrifuge is driven by an explosion-proof AC motor, and the inverter or clutch is activated.
b. The brakes are in the form of variable frequency energy brakes.
3 Industrial centrifuge operation
3.1 Preparation before starting up
a、Clean working place before starting up in order to eliminate obstacles, and check the parts below;
b、Turning the drum by hand shall not cause seizure or seizure;
c.、The bolts of all parts should be tightened without looseness;
d、Check whether the filter bag meets the material deliquoring requirements and must not be damaged;
e、The cover of the cabinet cover should be flexible and reliable;
f、Check that the connections are correct and reliable;
g、Connect the operation cabinet, control cabinet and main unit according to the random power line mark.
3.2 Starting up and operation
3.2.1 Frequency conversion start
(1) Turn on the power, open the control cabinet and the operating cabinet power supply. Then the inverter runs according to the preset parameters (starting time, speed section, braking time, speed display, etc.) (parameters can be modified, refer to the inverter manual), and the panel of the operation cabinet is shown in the figure.
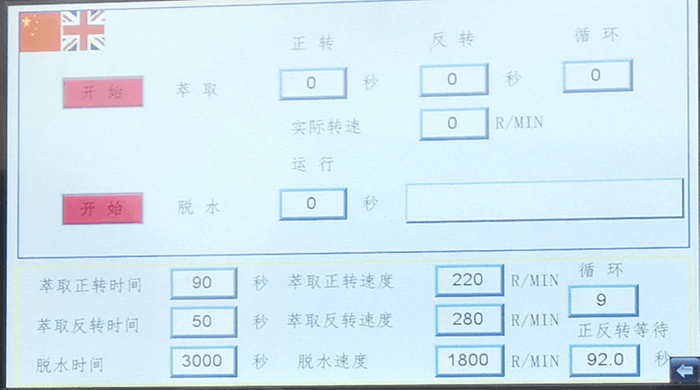
(2) Now, the extracted material is loaded into the filter bag, and the zipper is pulled into the centrifuge to check whether the charge is even. The upper part of the display is the display area and the lower part is the operation area.
(3) Close the top cover of the centrifuge and press the crimp. Make sure the outlet valve is closed, open the inlet tube valve, and add alcohol to the material that has not been extracted.
(4) Set up separating parameters, which includes the extraction forward rotation time (generally 60 seconds) extraction forward rotation speed (generally 200RPM), extraction reversal time (generally 60 seconds) extraction reversal speed (generally 200RPM), the number of cycles (generally 5 times), dehydration time (usually take 5 minutes), dehydration speed (take the corresponding model maximum speed), forward and reverse waiting time (usually take 30 seconds).
(5) Press the start button.
(6) Open the outlet valve after the extraction cycle to finish. And after all the extract is discharged (after it has to be drained), press the dehydration start button and the machine starts dehydration.
(7) After the dehydration is completed, release the lock handle after the device stops, open the flip cover of the centrifuge, and manually remove the filter bag. Pay attention to the protection of the filter cloth when unloading, in order not to cause damage to the material and vibration during the next use.
(8) Make sure the filter bag is intact, reload the extracted material, cover the cover and lock the handle to start the second working cycle.
(9) Notes: The speed increase (start) time and speed reduction (braking) time of the inverter are set internally. The users can make appropriate adjustment according to the actual situation, but it must be set by professional personnel. Please refer to the instruction manual of the inverter for the specific setting method.
Common Faults and Solutions
Faults | Parts | Causes | Solutions |
Abnormal shake | Drum unit | Uneven loading | Stir the extracted material to make the charge uniform |
The filter cloth (bag) is damaged or not properly leaked, which makes the drum lose balance. | Re-attach the filter cloth (bag) or replace the repair | ||
Spindle component | Severe wear or damage to the spindle bearings | Replacement bearing | |
Loose spindle nut | Fastening nut | ||
Base unit | The base is not installed horizontally or the foot nut is loose. | Adjust the horizontal fastening nut | |
Shock absorber damage | Replace the shock absorber | ||
Abnormal noise | Loose transmission parts | Tighten the loose parts | |
Leakage | Seal aging | Replacement seal | |
Excessive feed or filter cake containing too much liquid | Filter cloth (bag) | Filter cloth (bag) is not selected properly, Filter cloth (bag) is damaged or not fit properly |
Select the appropriate filter cloth (bag) to repair and replace the filter bag according to the nature of the material. |
Starting current is too large. Motor heating abnormality |
Transmission | Motor is defective | Repair or replace the motor |
Loading exceeds rated amount | Loading by rated capacity | ||
Parts are loose, detached or damaged | Fastening replacement parts |
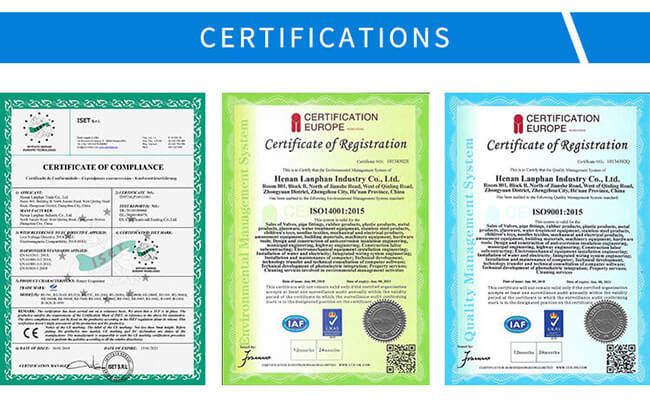
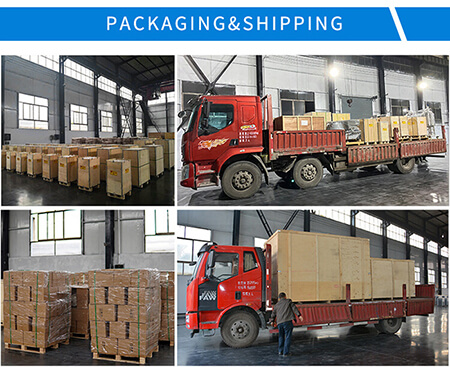
Pre-Sale Service
- Provide 24-hour technical consultation and reply;
- Provide professional quotation information;
- Provide detailed product performance specification;
- According to product’s using condition, technicians will offer rationalization proposals to assist clients to select proper product types;
- Provide other corollary equipment according to client requirements.
In-Sale Service
- With supervision from the source of products, the qualified rate of raw materials entering the factory can reach 100%;
- Whole manufacturing process are in strict accordance with promised procedure requirements, product qualified rate can reach100%;
- Provide product’s inspection record of key junctures to customers;
- Provide production schedule photos to customers at regular intervals;
- Package and transport of products are in strictaccordance with the export standard;
- Provide transportation schedule information to clients timely.
After-Sale Service
- Provide targeted installation video;
- Under the premise of correct installation, normal maintenance and using, we guarantee one-year warranty period;
- When warranty period has expired, our sold products enjoys lifetime guarantee repair, we only charge cost price for changing product’s standard component and sealing component;
- During installation and adjustment period, our after-sale service staff will communicate with customers frequently to know product’s running state in time. Assist customers to install and adjust products until customers are satisfied;
- If product has malfunction during operation period, we’ll offer you satisfied answer in time. We’ll reply you within 1 hour and provide solution or send staff to spot within 24 hours after receiving maintenance notification;
- Lifelong free technical support. Conduct satisfaction survey and inquiry equipment running condition to clients by telephone or e-mail semiannually from the first day of equipment running, put on records of acquired information;
- Provide assistance in solving problems such as equipment damage in the transport.