Description
Product Introduction
Today’s wet granulation equipment has developed to high-speed wet granulation. In recent years, it has become the fastest growing, most widely used, and most economical granulator. It combines the mixing and granulation processes together and is carried out in a fully enclosed container. It is characterized by saving time and meeting GMP requirements, good mixing effect, high production efficiency, good particle and sphericity, good fluidity, easy cleaning, and no pollution. It has the characteristics of stable content and low energy consumption. It is a kind of equipment with large granulation capacity, high speed, good granular and low energy consumption. It is well received by most users. Among the current solid granulators, high-speed wet granulators occupy more than 70% of the market share.
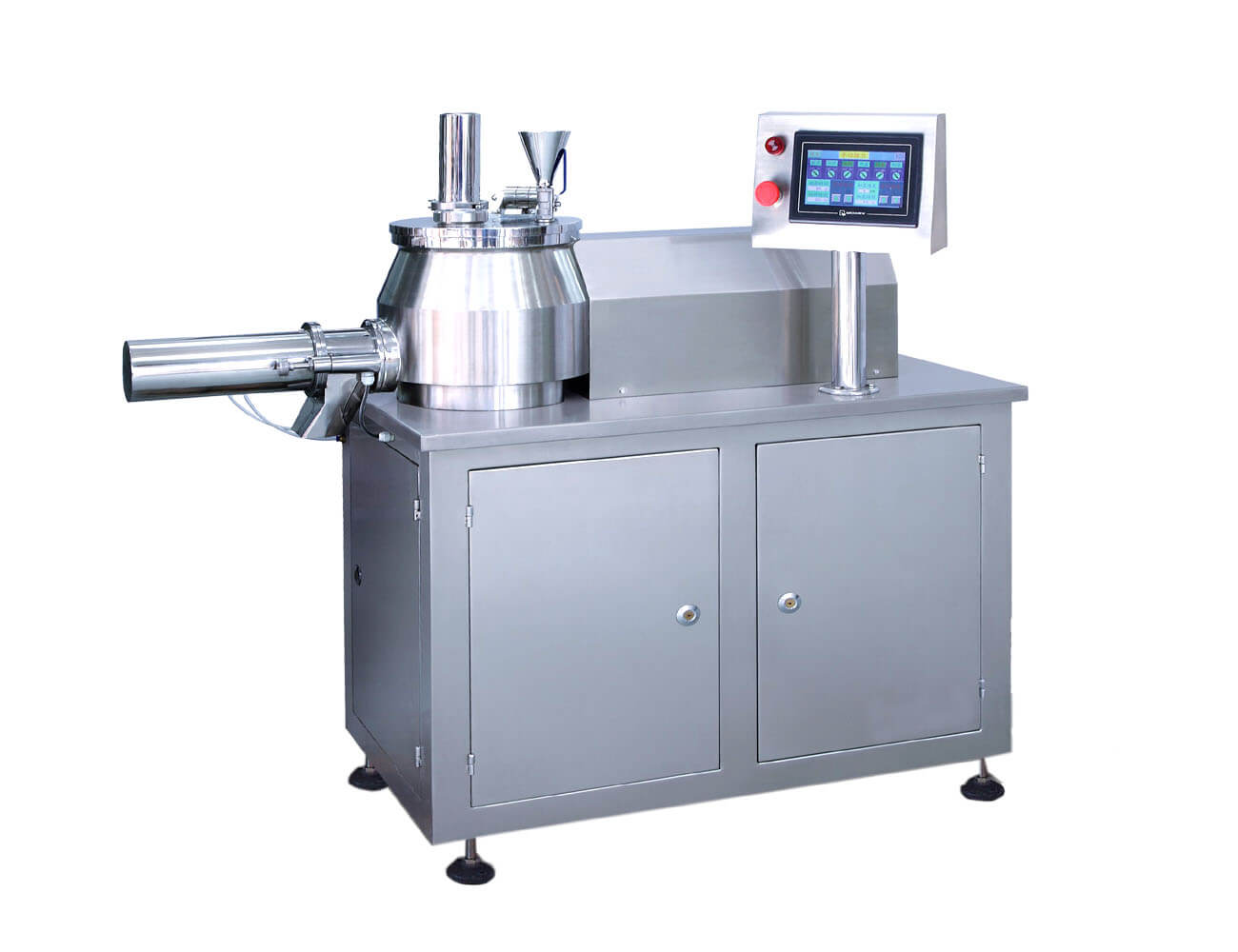
Product Application
The high-speed mixing granulator uses high-speed side slices and bottom plane rotating blades to mix various powders of different particles in the case of cross rotation. Because the bottom, middle and upper parts of the mixing tank are parallel and the cylindrical and conical design, the powder raw materials continue to be brought to the center of the tank during the mixing process, and the strong and powerful shearing and breaking force of the secondary shaft will form up and down and rotating flows in the tank to achieve the granulation effect. Finally, it is discharged from the discharge port, and the rotation speed of the stirring and cutting flying knife is changed to obtain equipment of different sizes of particles. It is widely used in the pharmaceutical, chemical and food industries.
Product Features
1. Short granulation time and energy saving.
2. The entire operation has strict safety protection measures.
3. Compared with the traditional process, the adhesive is reduced by 25%, and the drying time is shortened.
4. This machine adopts horizontal cylindrical or conical structure, users can choose freely.
5. There is no dead corner on the inner surface of the equipment, and it works in a closed state and meets the requirements of “GMP”.
6. The finished granules have uniform texture and good fluidity, providing ideal granular raw materials for the tableting process.
7. Each batch is dry-mixed for only 2 minutes, and granulated for 1 to 4 minutes. The efficiency is 4 to 5 times higher than that of the traditional process.
8. When there is a big difference between the main drug and the excipient, the uniform combination can still be achieved without delamination.
The Purpose of Granulation
- Improve fluidity, which is convenient for packaging and tableting.
- Prevent the segregation of each component due to differences in particle size or density.
- Prevent dust flying and adhesion on the wall.
- Adjust the bulk density and improve the dissolution performance.
- Improve the uniformity of pressure transmission in tablet production.
- It is easy to takeandcarry, and increase the value of goods.
Product Parameters
Technical Specifications
Model | A | B | C×D | E | F |
50 | 320 | 950 | 1250×800 | 970 | 1650 |
150 | 420 | 1000 | 1350×800 | 1050 | 1750 |
200 | 500 | 1100 | 1650×940 | 1450 | 2050 |
250 | 500 | 1160 | 1650×940 | 1400 | 2260 |
300 | 550 | 1200 | 1700×1000 | 1400 | 2310 |
400 | 670 | 1300 | 1860×1100 | 1550 | 2410 |
600 | 750 | 1500 | 2000×1230 | 1750 | 2610 |
Name | Model | ||||||
50 | 150 | 200 | 250 | 300 | 400 | 600 | |
Volume(L) | 50 | 150 | 200 | 250 | 300 | 400 | 600 |
Output(kg/batch) | 15 | 50 | 80 | 100 | 130 | 200 | 280 |
Mixing speed(r.p.m.) | 200/400 | 180/270 | 180/270 | 180/270 | 140/220 | 106/155 | 80/120 |
Mixing power(kw) | 4/5.5 | 6.5/8 | 9/11 | 9/11 | 13/16 | 18.5/22 | 22/30 |
Cutting speed(r.p.m.) | 1500/3000 | 1500/3000 | 1500/3000 | 1500/3000 | 1500/3000 | 1500/3000 | 1500/3000 |
Cutting power(kw) | 1.3/1.8 | 2.4/3 | 4.5/5.5 | 4.5/5.5 | 4.5/5.5 | 6.5/8 | 9/11 |
Compressed air consumption(m³/min) | 0.6 | 0.9 | 0.9 | 0.9 | 1.1 | 1.5 | 1.8 |
Weight(kg) | 500 | 800 | 1000 | 1300 | 1800 | 2200 | 2600 |
Price: 50L-55,000 yuan; 150L-78,000 yuan; 200L-85,000 yuan;
250L-92,000 yuan; 300L-110,000 yuan; 400L-150,000 yuan; 600L-200,000 yuan;
Generally speaking, the granules made by wet mixing granulator have uniform particle size distribution and perfect structure compared with other traditional granulation processes. However, the granulation products are affected by many factors. The specific influences are as follows.
- The influence of the rotating speed of the stirring blade and the cutting knife
It can be said that the size and distribution of the particle size is directly related to the rotating speed of the stirring blade and the cutting knife. When the rotating speed of the cutting blade is slow, the particle size becomes larger, and when the rotating speed is fast, the particle size becomes smaller; When the rotating speed of the stirring blade is slow, the particle size is small, and when the rotating speed is fast, the particle size is large, and the two functions are opposite.
- The influence of mixing and granulating procedures and time
In the operation of the high-speed mixing granulator, the rotation of the stirring paddle causes the material in the pot to roll to the space, so that the material at the bottom of the pot rotates and throws up along the wall of the pot. This action pushes the soft material towards the fast cutting knife one after another, and is cut into particles of different sizes. As the particles roll over each other for a period of time, they are rounded and gradually formed into a spherical shape. It can be seen that the speed and time of the stirring blade and the cutting knife affect the granularity of granulation.
- The influence of material and concentration
In the production of wet mixed granulation, alcohol granulation or dextrin adhesive granulation are commonly used, but there are certain differences between the two. Alcohol is commonly used for granulation, and the granules produced are small, fine and easy to dry. Because alcohol does not have viscosity and it has a loosening effect, this method is ideal for granulating traditional Chinese medicines with high viscosity. When dextrin is used for granulation, the particles produced are large and coarse, and the drying is slow. This is because dextrin is viscous and has a polymerization effect. This method is ideal for western medicine without viscosity.
In addition, whether the concentrated extract is diluted as a material, or dextrin or other adhesive as the materials, when producing smaller particles, the slurry concentration of the material can be thinner, and when larger particles are required, the slurry concentration of the material can be slightly thicker.
Causes and solutions of blockage in the production process of granulator
- Inappropriate gap of the mold roll
The gap between the mold rolls is too large, causing the material layer between the mold rolls to be too thick and unevenly distributed, and the pressure roll is easy to slip due to uneven force. Once the squeezing force of the mold roll on the material is less than the resistance of the inner wall of the die hole to the material, the material cannot be squeezed out and the machine will be blocked. In order to reduce machine blockage, attention should be paid to adjusting the gap between the mold rolls during production. When adjusting, it is the best that the pressure roller and the ring mold form a state of seeming to depend on or rotate but not to. According to the observation, the gap is generally 3-5mm. Among these, the granulating workers’ experience and the adjustment hand feel is quite important.
- The influence of steam
The most ideal production condition elements in the granulated feed production process are: the raw material moisture is appropriate, the steam quality is good, and there is sufficient conditioning time. The correct use of dry saturated steam for granulation can effectively improve the output of the granulator and the quality of the pellets. To ensure good pellet quality and high output, in addition to the normal operation of the various transmission parts of the pellet mill, the quality of the dry saturated steam entering the pellet mill conditioner should also be ensured. Applicable saturated steam has a softening and lubricating effect in the granulation process, which can increase productivity, reduce frictional heat energy, and extend the service life of ring mold; it can reduce power consumption, promote starch gelation, and fibrous fiber bonding; It can increase the forming rate of particles, reduce the powder, make the material appearance smooth and tidy, thus improving the competitiveness of products.
The quality of steam is poor, so that the moisture content of the material is too high when out of the conditioner, and the mold hole is easily blocked when entering the granulating cavity, and the pressure roller slips, resulting in the machine blockage.
Specific manifestations are as follows:
①Insufficient steam pressure and high moisture content make the material absorb too much water. At the same time, when the pressure is low, the temperature is also low when the material is quenched and tempered, starch cannot be gelatinized well, and the granulation effect is poor;
②The steam pressure is unstable, suddenly high and suddenly low, and the material conditioning is unstable, resulting in large fluctuations in the current of the granulator. Uneven material thirst is also easy to cause the machine to block in the normal production process.
The granulating worker must pay attention to various factors such as steam pressure and the feed volume of the conditioner at any time to avoid excessively high moisture content in the material caused by the steam pressure and water content. At the same time, in order to reduce the number of blockages caused by steam quality, the boiler room should provide high-quality and stable dry saturated steam. During the production process, the granulating worker should pay attention to the moisture of the material after conditioning at any time. It can be judged by a simple method. The specific method is: grab a handful of the material out of the conditioner and hold it into a mass with hand, and it is proper to let it go and just spread it out.
- The influence of conditioning effect
To make pellet feed meet the competitive demands of the market, it is necessary to ensure its high quality. The conditioning effect of the material before granulation is very important, because it directly affects the output of the granulator and the quality of the granules, especially the stability of special aquatic products in water is an important indicator. If the material cannot be fully conditioned and matured before granulation, its water stability index will be difficult to guarantee. The so-called conditioning is the pretreatment of the powdered material before granulation, which is the process of fully stirring and absorbing the powder to be granulated and an appropriate amount of steam in the conditioner. Select the conditioning equipment that meets the technical requirements, so that the material can be fully stirred and mixed with steam in the conditioner to achieve the function of softening the material and gelatinized starch, which is conducive to the compaction and formation of the powder and the production of qualified products. The conditioner needs to have a longer time of heat preservation, heating and humidification, and the number of layers can be combined and installed as needed to ensure that the material fully meets the requirements of conditioning, improve the surface and internal quality of the granular material, and improve its water resistance in water. The most advanced method at this stage is the use of modulator + quality assurance device + modulator, which can achieve the most ideal conditioning effect.
Through on-site debugging, the number of blockages of the pellet machine can be reduced, which can be solved by adjusting the steam. Since the boiler equipment has been finalized, the steam provided has been determined. Pay attention to the treatment method of water vapor in the steam pipeline, try to remove the condensed water in the steam pipeline, and the steam pressure of the front end of the modulator should be very stable.
Reviews
There are no reviews yet.